Blog
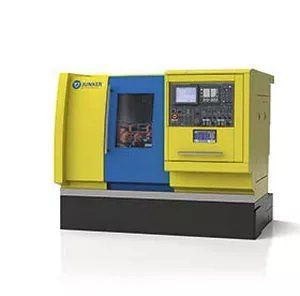
Grinding instead of turning in series production. When manufacturing small components with a diameter of between 2 and 20 mm, the GRINDSTAR grinding machine from Junker offers an economical alternative to turning. From batch sizes of 200,000, short cycle times and a long workpiece service life can drive down costs per workpiece by up to 25%. Its high productivity makes the GRINDSTAR a particularly interesting alternative, also for large-scale series manufacturing in the automotive industry. The innovative grinding method enables the entire workpiece contour to be ground in just a single processing operation. In addition, grinding involves far lower cutting forces than those occurring during turning, allowing faster grinding of workpieces. The third success factor of this machine is the perfect coordination it allows between workpiece, abrasive and machine. All three factors act together to enable a significant increase in productivity. The GRINDSTAR is up to three times faster than a lathe. The automotive and supply industry demands high piece numbers with the fastest possible turnaround. And this is precisely where the strengths of GRINDSTAR are brought to bear: From material cut-off through profiling to ejection, every work step is covered in a single machine. This enhances process reliability and minimizes machine downtime. As a result, GRINDSTAR achieves an impressive availability level of over 96% and a long tool service life. Due to its innovative cooling system, the grinding wheels work precisely and to a consistent standard of quality – for up to six months or a production volume of 300,000 pieces and over. Grinding instead of turning also impacts positively on the quality of workpieces, with significantly improved dimensional accuracy and excellent surface quality. The manufacture of burr-free parts during grinding is 100% guaranteed. And unlike turning, no chip impressions are created. The two profile grinding wheels used in the GRINDSTAR require no dressing and use an innovative lubrication method. The flushing system used prevents particles being deposited on the grinding wheels, eliminating the need for the reworking process frequently required when turning. This reduces the production time required and saves the need to invest in additional machinery, for instance for surface grinding or polishing. When it comes to the choice of material, the GRINDSTAR offers maximum flexibility. Of particular interest for the automotive industry with its increasing demand for lightweight technology: Curable plastics and glass fiber-reinforced plastics can also be quickly and reliably ground. Materials which can be ground include high-alloy tough steels, hardened materials and even ceramics. CBN or diamond can be used as abrasives. Junker knows which grinding wheel specification is the most suitable for which material. Because with GRINDSTAR, the company offers far more than just a grinding machine. Behind it is a concept permitting adaptation by experts based on their many years of experience. So that every GRINDSTAR is precisely adapted to the specific needs of each customer. From profiling through coating of the grinding wheels to the individual machine settings – Junker uses its in-depth expertise to plan the entire production process. This eliminates the need for laborious and costly test runs by the customer. The GRINDSTAR is quickly and simply up and running, entirely in keeping with the plug and play principle.
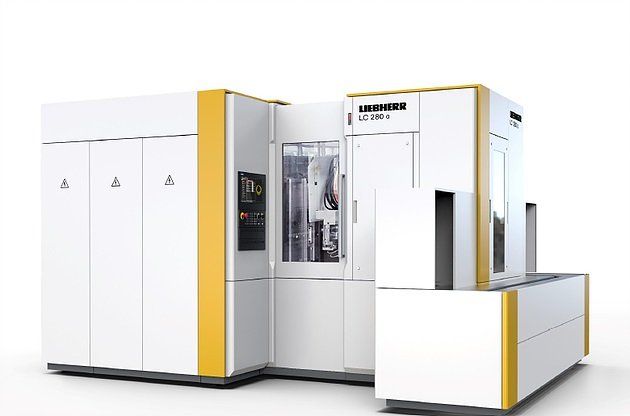
A new generation of gear hobbing machines with increased performance & short delivery times. The LC 280 α provides Liebherr quality with maximum flexibility and short delivery times. Liebherr have developed a new generation of gear hobbing machines with shorter lead times. The criteria for an investment decision regarding a new gear cutting machine are primarily quality, maximum flexibility, and at the same time maximum productivity with low procurement costs. For the end user it is vital to have a machine that can process a diverse range of tasks and how efficiently the tasks can be completed. The LC 280 α was developed precisely for these requirements.
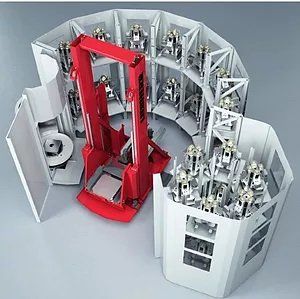
The benefits of the Liebherr Rotary Loading System Liebherr offers a wide range of automation systems supporting modern high-efficiency production environments. Their solutions not only reduce production costs but are also able to quickly respond to fluctuating production volumes. Liebherr automation systems are designed for cost-effectiveness, ease of use, quality and reliability in combination with a high degree of flexibility.For pallet handling systems, Liebherr offers the RLS rotary loading system as a supplement to the linear PHS. It is the ideal solution for an economical entry into high-efficiency machining via pallet handling. Economy A basis for cost-effective machining is optimizing the feeding of parts in and out of the machining center. Hand-loaded or semi-automatic machines are limited, while the Liebherr RLS rotary loading systems normally enable spindle efficiencies above 90%. With the introduction of lights out production, the need for manpower is reduced.In essence, we are allowing the investment to pay for itself quickly. Flexibility With its modular design, the Liebherr RLS rotary loading system offers a high degree of flexibility. It offers a versatile platform that can be configured to a variety of machine setups for different requirements. User-Friendly The proven Soflex PCS cell controller is user-friendly and offers integrated order planning. Further, it is completely open for expansion. In the basic version, NC program and tool management remain on the machine, while the cell controller manages pallets and order planning. This allows operators to continue working in a familiar machine environment. Short commissioning time, high acceptance and fast production start-up are the results. Quality and Reliability Quality is the top priority for Liebherr. When producing our products, every stage is monitored ensuring world-class products with the highest reliability and service life. The quality management system of the entire production process at Liebherr-Verzahntechnik GmbH is certified in accordance with DIN EN ISO 9001:2008. In addition, our product development benefit from the Liebherr group‘s diversity and many years of in-house experience with state of the art manufacturing technologies.